PROCESSES
DESIGN
In eyewear development, product conception is often the most complicated stage, but also the most exciting. LEM offers assistance right from the inception of the product, blending design and technical requirements to incorporate specific features.
LEM engineers provide support by adapting the specific customer approach to the development process:
3D to 3D printed prototype
This is an all-digital approach suitable for customers with in-house 3D development capabilities. LEM makes all the digital changes needed for optimal fit and moldability of the finished product.
Emotional 2D sketch to 3D
This is a comprehensive approach from the transformation of the original idea to 2D technical drawings, a handmade prototype and, lastly, a 3D printed prototype through reverse engineering.
Everything in between
The most common approach, which applies the best of the two worlds depending on the customer’s specific needs.
ENGINEERING
Our workflow is managed entirely in-house by our own engineering department, from concept analysis to mold-ready 3D files.
We therefore have a track record of confidentiality, optimal scheduling and faster than average time to market.
PROTOTYPING
The creation of the prototype is a “unique” blend of our two core skills: craftsmanship and technology.
Craftmanship is our legacy core value developed over decades of modeling and moulding ideas into real life objects.
Technology is the force multiplier that allows a single-piece master model to be engineered and produced on a larger scale.
LEM has built an internal Digital Fab, which uses 3D scanning and printing to turn the single-piece golden sample into a wearable product. Every single adjustment made to the CAD project is traceable and reversible, enabling us to submit different versions of the same product. Meanwhile, our expert technical team will provide the customer with a finished sample whose characteristics will be almost the same as the final product.
MOLD DEVELOPMENT
Mold development is the cornerstone of any injection-molded frame.
Once the final 3D file has been reviewed and approved, production of the mold is assigned to one of a small set of mold makers selected from among the most qualified in the industry.
When the mold is ready, we evaluate the results through detailed metrological inspection to ensure that the injected part conforms to specifications.
Once all the tests have been completed, the mold is commissioned in our injection farm.
INJECTION DEPARTMENT
In recent years we have invested continuously in injection technology.
Today our injection farm operates 18 injection molding machines of various sizes, enabling us to mold everything from the tiniest part to large pieces such as ski goggles.
Over time, we have developed consolidated expertise in over-injection and bi-injection processes, where we combine different innovative materials in the same frame.
Driven by our passion for innovation, we constantly monitor developments in different industries and, where applicable, transfer the best new technologies into eyewear manufacture.
AUTOMATION
Collaborative robotics has been a part of LEM for many years.
Cobots have made our processes more efficient, consistent and productive. Improved ergonomics and the assignment of repetitive tasks to cobots have significatively improved working conditions for our operators.
Our collaborative robotic arms are used in many machine tending applications such as lens edging, laser marking and many others.
Collaborative robotics is the cornerstone for our transformation path toward Industry 4.0.
PAINTING AND ESTHETIC TREATMENTS
Frame painting is the core of injected-frame manufacturing.
It is at this stage that the injected parts are transformed into works of art, through a rare combination of craftmanship, technology and years of experience in frame coloring.
In addition to classic painting, LEM has developed many specific treatments such as masking, laser paint removal, multilayer metal coating, with many others coming soon.
Recent additions include vacuum heat transfer and frame wrapping.
FINISHES
LEM has developed an extensive range of final coatings for its eyewear, from classic matt and gloss finishes to more complex solutions such as rubberized, soft touch and semi-gloss finishes.
LENS EDGING
LEM processes all types of lenses, mainly nylon and polycarbonate, using three fully automated CNC machines to guarantee absolute precision and replicability with each cut.
We run a strict lens quality inspection process adopting statistical control, which covers prism strength, spherical strength and transmittance.
LASER MARKING
LEM uses a variety of laser sources such as CO2, YAG and UV to be able to process different surfaces including lenses, paint, raw plastic and metal.
We recently combined laser etching with robotics, to become one of the few companies that also perform cosmetic treatments with lasers, guaranteeing constant precision at every stage in the process.
ASSEMBLY AND QUALITY CONTROL
This is the final stage in the whole production process, where our most skilled operators assemble the product – lens glazing, rubber-components gluing – and fine-tune the whole assembly. This is followed by the final quality control, a multiple-stage process.
Some quality checkpoints are inspected on every frame, others are inspected on a selected number of units in accordance with our SPC tables. In addition to these inline checks, we also perform destructive tests to guarantee that frame performance complies with specifications.
Destructive tests include temple open-and-close cycles, overflex tests, paint adhesion, as well as aging and weathering tests in saline fog and UV ray climate rooms to simulate wear over the product life cycle.
Every test is digitally filed in the internal quality journal, to guarantee test traceability of each production batch and make results available upon request to customers.
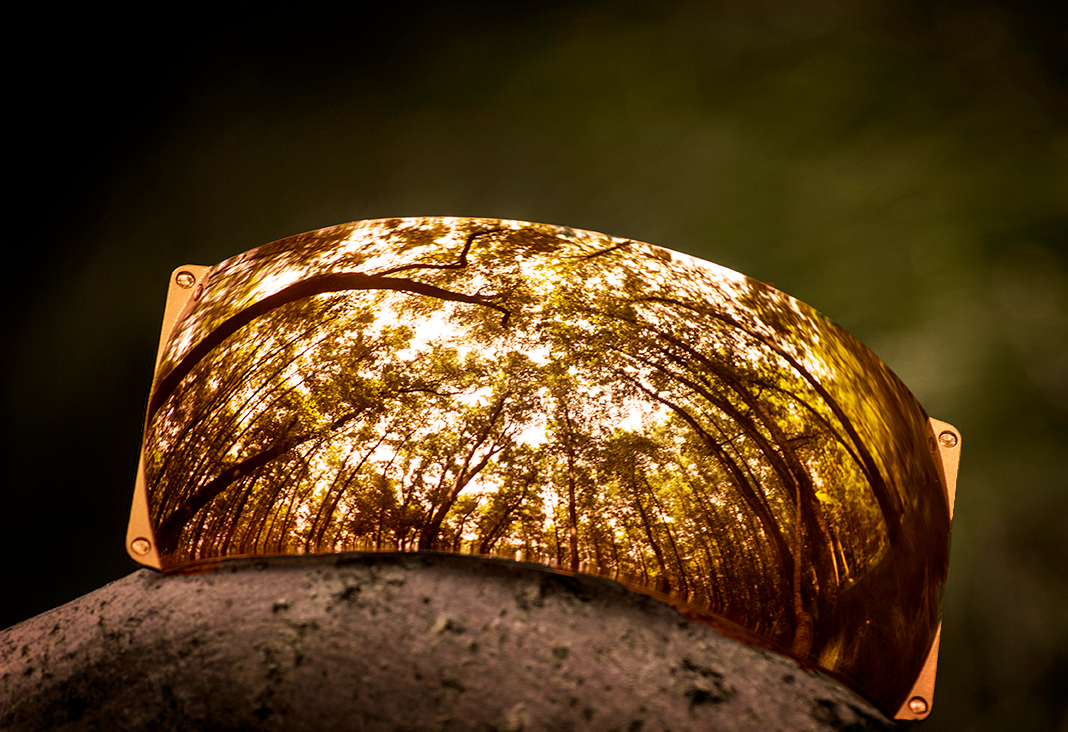
CONTACT